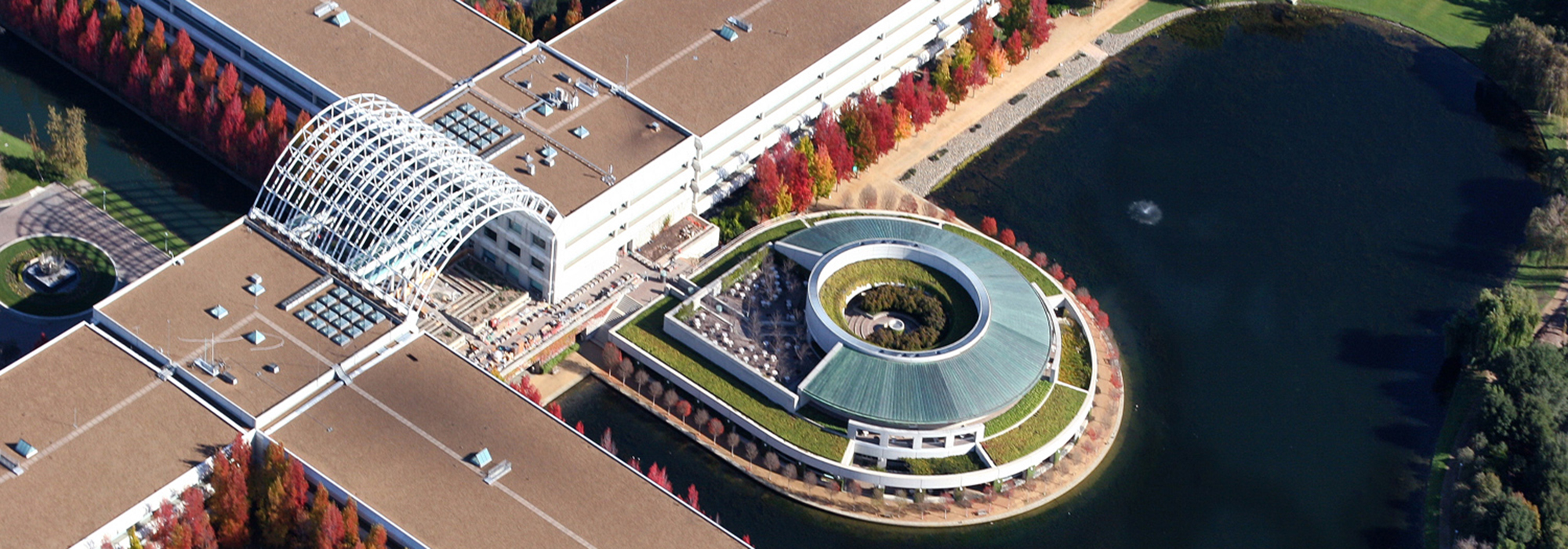
Roofing
Roofing Applications
Monolithic Membrane 6125® (MM6125®) is a hot applied rubberized asphalt for use in waterproofing. MM6125® is a thick, tough, flexible and self-healing membrane. It has been successfully used worldwide by leading architects, engineers and owners on all types of horizontal and vertical structures including plazas, parking decks, fountains, water basins, planters, tunnels, bridges, mud slabs, foundation walls, roofs and vegetative roofs. MM6125® has an unbeatable track record of more than 60 years.
Hydrotech's Protected Membrane Roof Assembly (PMR)...
Conventional thinking in roof design:
As building structures became bigger, and the corresponding larger areas could not be effectively covered with steep roofs, the technology of the flat roof evolved. The water shedding slope was gone and roofs required a new element - waterproofing. To meet this requirement, the roofing industry began to mop asphalt membrane directly to the roof deck. As fuel costs increased back in the 1940's another demand was placed on the roof - energy efficiency. The need to counter energy loss dictated the addition of roof insulation. Since insulating materials of four decades ago were not water-resistant, the insulation had to be placed under the waterproofing membrane for protection. This system became known as the conventional insulated built-up roof system. With the conventional roof, the insulation is protected from the exterior environment; however, the membrane is separated from the roof deck. Because it is no longer kept within the moderate temperature range that is near the building's temperature, the membrane is subject to a new set of conditions and stresses.
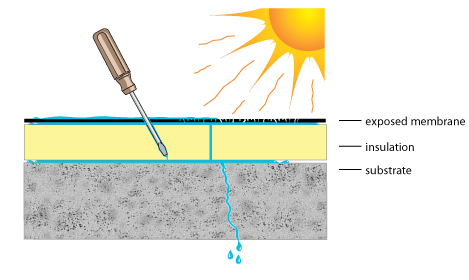
Conventional roofs are susceptible to...
A conventional roofing arrangement can leave the waterproofing membrane vulnerable to extreme and often sudden temperature changes, high summer roof temperatures, lower winter temperatures, freezing puddles, ultraviolet rays, physical abuse from heavy foot traffic and routine maintenance. Exposure to all of these elements weakens the integrity of the membrane. Once the membrane is compromised, moisture will eventually enter the insulation and cause a loss in its thermal efficiency. THERE IS A BETTER WAY...
Typical Roofing Applications
Unconventional common sense in roofing technology...
The Protected Membrane Roof (PMR)...
A better way is possible because of DuPont STYROFOAM™ brand insulation, a closed cell polystyrene that is highly moisture-resistant. Placed on top of Hydrotech's Monolithic Membrane 6125®, it offers protection from the harsh roof environment. This arrangement of roofing materials - roof deck, waterproofing membrane, moisture-resistant insulation - is commonly referred to today as the Protected Membrane Roof (PMR) or Insulated Roof Membrane Assembly (IRMA). With such roofs, the membrane's temperature range and rate of temperature change are drastically reduced. By simply reversing the insulation and the membrane - insulation on top of the membrane rather than beneath - the cause of many roofing problems can be eliminated.
Benefits
Advantages of the PMR Assembly...
In conventional roofing the exposed membrane can be easily damaged by physical abuse; abuse caused by other trades during construction or after from maintenance to roof top HVAC units, or the occasional arrow shot in the air. Obviously, in a PMR assembly, the insulation and ballast layer on top of the membrane helps to protect it from physical abuse.
Mother nature can be brutal too; from large temperature swings from day to night, freeze-thaw cycling, UV and ozone.
A study done by the U.S. Army, Corps of Engineers in the 1970's showed that on a PMR installation in Alaska, the roof membrane stayed within 8°C of the deck temperature year round.